Optimum Heat Source Control System
Heat Source Equipment Control Technology/Optimal Operation Technology
What is heat source equipment control and optimal operationtechnology?
Control technology that enables entire system optimal and energy-saving by providing operation group for various heat sources and auxiliary equipments following fluctuating outdoor or indoor load.
- Want to reduce CO2 and enhance energy efficiency
Overview
Control System that Maximizes the Energy-saving Impact for a Heat Source System
The operation configuration for maximizing the energy-saving impact on Heat Source systems varies depending on the conditions of outside air and loads. As system performances have been enhanced and control technologies have advanced, more complex configuration parameters are required. Manual configuration cannot always optimize total energy-saving operations for facilities in accordance with the ever-changing outside conditions and complicated parameters.
Optimum heat source control system maximizes the impact of energy saving for the entire system by modifying setting values with real- time caluculation.
Features
-
Achieving optimal control
Based on the results of computational optimization with the HSSsim Heat Source simulator, the system delivers optimal control in accordance with the ever-changing outside conditions.
-
Reliable operation and high-level security with various control modes
PLC constantly monitors and makes sure that the control operation is not interrupted when a system goes down or a computer freezes.
When the computer is shut down, the system automatically switches to the PLC individual operation mode (PLC mode) to continue the control operation. It can be also switched to the PLC mode manually. These features enables you to keep running operations such as updating optimal control tables or computer maintenance without turning off devices. -
Real-time energy saving display
The system provides a real-time display of the computed volume of energy savings relative to a reference system.
(Comperative system: Conventional control methods, e.g. rated load operation) -
Stable operation at high load up rate using the operation mode
When the load-up rate is high such as in the morning time in summer, the number of units is controlled in accordance with load-forecasting data of 0 to 60 minutes ahead. This mode helps to improve response to loads.
-
Monitoring function
It displays a list of measured values and alarm data to be sent to PLC.
-
Optimal control planning including secondary chilled water temperature
We offer assist software that helps you develop an optimal control plan including secondary chilled water temperature in addition to optimal control on the primary heat source.
The assist software enables you to make complicated input conditions into simple entries that are given into HSSsim including factors on the secondary side. It is also designed to classify a large volume of output data collected from computation data including the secondary chilled water and to reflect it in charts. The assist software improves the operability of HSSsim and helps you plan design details.
Screenshot of energy saving volume comparisonScreenshot of energy saving volume comparison
Sample of the operation mode for high load up
-
Compatible with various heating equipment
Optimizing the control of systems containing a wide variety of heat source equipment including inverter turbo chillers, constant speed turbo chillers, double bundle turbo chillers, gas absorption chillers, waste heat injection type absorption chiller, air-cooled chillers, hot water heaters and thermal storage tanks.
HSSsim, heat source simulator
- The heat source simulator, HSSsim, is energy simulation software that supports various heat source systems.
- With its nonlinear mathematical programming it can perform computational optimizations.
- Use of HSSsim from the planning phase enables you to plan a composition with various devices and detailed control methods beforehand.
- The planning results are saved as optimal control data in the heat source monitor and used for control operations. (HSSsim is used only at the planning phase. It is not used with facilities at production lines once operation starts.)
Heat source monitor
- It saves, as optimal control data, the planning results from HSSsim.
- It collects measured values including outdoor air conditions and operation status from GPPECO.
- It calculates optimum operation conditions based on the collected measured values and the optimal control data from simulations.
- It reflects the calculated optimal operation conditions in control operations in a safe manner.
- It monitors heat source facilities with measured values and trends of energy-saving results from PLC (Programmable Logic Controller).
- It estimates real-time optimal setting values based on the measured values and the optimal control data from the heat source control system (Programmable Logic Controller).
GPPECO, heat source optimal control software
- It sends the collected measured values such as outdoor air conditions and operation status to the heat source monitor.
- It collects optimal setting values from the heat source monitor and applies for control operations.
- It is compatible with the central monitoring system and allows the conventional system to be easily renewed because the heat source monitor uses a standard PLC.
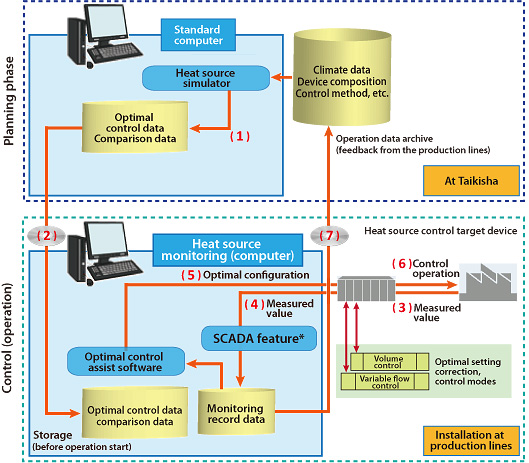
Plan |
|
---|---|
Operation |
|
Benefits
Effect of the Optimum Heat Source Control System
- With setting values (optimal control data) based on simulations, the system maximizes the impact of energy saving of the heat source system.
- It contributes to reducing running costs and CO2 emissions.
Calculation Example
In comparison with the conventional heat source control system, the annual cold/heat energy source is:
Reduced to 80% with the Optimum Heat Source Control System I *1)
Reduced to 72% with the Optimum Heat Source Control System II *2)
-
*1)System I: Optimal control operation to the primary heat source device
-
*2)System II: In addition to the system I, optimal control operation including the secondary chilled water temperature
Comparison of heat energy sources depending on the control method (estimation)