Quality Management
Value Creation Foundation for Quality
Basic Quality Philosophy
Based on our mission statement of “Customers First,” and guided by our Quality Management Vision and the guidelines for its realization, we contribute to the creation of an optimal environment and the development of society by providing high-quality systems and services through technologies that meet customer needs.
Quality Management Vision
To realize a “Customers First” approach, it is essential to establish quality assurance in work processes. At Taikisha, we strive to provide equipment that satisfies our customers in terms of functionality, price, and reliability.
Guidelines for the realization of Taikisha’s Quality Management Vision
- In order to earn the trust and meet the expectations of our customers, we work to accurately grasp their needs and provide systems that offer performance with high customer satisfaction.
- We ensure quality in each process based on our quality assurance system chart. Furthermore, in light of technological advances, increasingly complex systems, and heightened awareness regarding quality, we place emphasis on foolproof and fail-safe designs and construction to ensure safety and reliability for our customers.
- We will continue to take on the challenge of developing innovative technologies by making full use of our engineering expertise in the fields of energy, air, and water.
Quality Policy
Green Technology System Division
- Basic Philosophy
- With the aim of realizing a sustainable society, we at the Green Technology System Division will improve the quality of our design and construction processes and provide technologies that reduce environmental impact in order to deliver customer services that satisfy all stakeholders.
Paint Finishing System Division
- Basic Philosophy
- We at the Paint Finishing System Division will construct and implement a division level environmental management system based on a correct understanding of the company’s Mission Statement, Corporate Philosophy and Management Vision, and will strive to improve this system through regular management reviews in order to contribute to all stakeholders.
Quality Management System
Quality Control System Chart
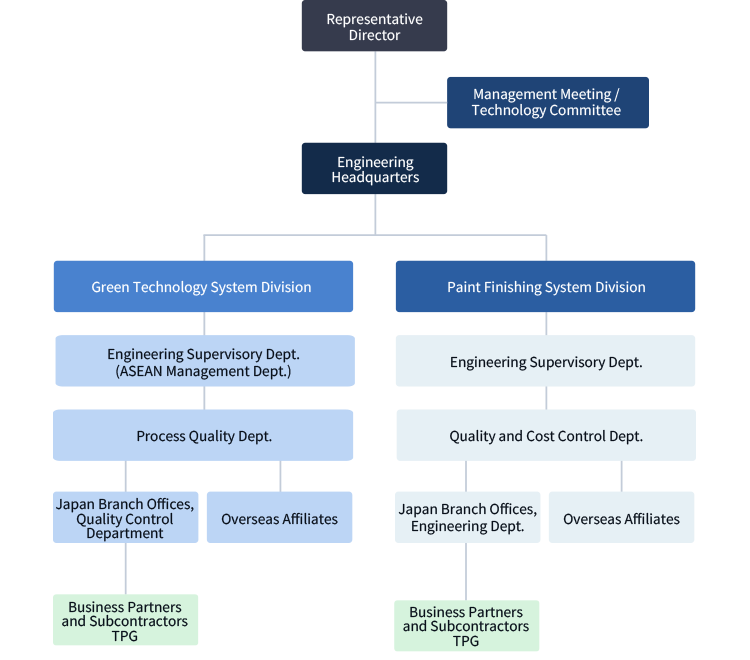
Taikisha has established a quality management promotion system based on ISO 9001 for the purpose of quality assurance, with our Green Technology System Business and Paint Finishing System Business as core businesses.
We have established the Technical Committee at the headquarters and a quality control department in each division, and these are responsible for overall management as well as providing support for the quality assurance activities of individual branches and offices.
ISO9001 Certification Obtained
Green Technology System Division
Facilities | Head Office / Tohoku Branch Office / Tokyo Branch Office / Chubu Branch Office / Osaka Branch Office / Kyushu Branch Office / Marketing and Development Dept. / Research & Development Center |
---|---|
Certifying organization | ANAB (USA) |
Inspecting organization | ABS Quality Evaluations, Inc. (USA) |
Certificate number | 32928 |
Paint Finishing System Division
Facilities | Head Office / Tohoku Branch Office / Tokyo Branch Office / Chubu Branch Office / Osaka Branch Office / Kyushu Branch Office |
---|---|
Certifying organization | JAB (Japan), UKAS (UK), ANAB (USA) |
Inspecting organization | Perry Johnson Registrars, Inc. (USA) |
Certificate number | C2022-04576 |
Taikisha Group’s Status of Acquisition of ISO9001 Certification
Asia
Country Name | Company Name | ISO9001 |
---|---|---|
Thailand | Taikisha (Thailand) Co., Ltd. | ○ |
Greater China | WuZhou Taikisha Engineering Co., Ltd. | ○ |
Greater China | Tianjin Taikisha Paint Finishing System Ltd. | ○ |
Philippines | Taikisha Philippines Inc. | ○ |
Vietnam | Taikisha Vietnam Engineering Inc. | ○ |
India | Taikisha Engineering India Private Ltd. | ○ |
India | Nicomac Taikisha Clean Rooms Private Limited | *1 Acquisition scheduled for 2026 |
Indonesia | P.T. Taikisha Indonesia Engineering | ○ |
Singapore | Taikisha (Singapore) Pte. Ltd. | ○ |
Malaysia | Taikisha Engineering (M) Sdn. Bhd. | ○ |
Cambodia | Taikisha (Cambodia) Co.,Ltd. | *2 |
Lao | Taikisha Lao Co., Ltd. | *2 |
South Korea | Taikisha Korea Ltd. | *1 Acquisition scheduled for 2027 |
Taiwan | Taikisha (Taiwan) Ltd. | ○ |
North America
Country Name | Company Name | ISO9001 |
---|---|---|
USA | Taikisha USA, Inc. | ○ |
South America
Country Name | Company Name | ISO9001 |
---|---|---|
Brasil | Taikisha do Brasil Ltda. | *2 |
Europe
Country Name | Company Name | ISO9001 |
---|---|---|
Germany | Taikisha Deutschland GmbH | ○ |
-
*1Currently operating own in-house ISO-compliant system
-
*2Comply with the management system of the branch in charge of each property
Design and Construction Quality Improvement Activities
- Ensuring construction quality
At the design stage, we aim to plan and provide systems that meet the needs of society, and to provide equipment and systems that customers can rely on, utilizing fail-safe and foolproof concepts. In terms of construction quality, we are pursuing quality assurance based on the market, and we are moving forward with construction activities with an emphasis on function, price, and integrity in order to win the lasting trust of all stakeholders.
Specifically, our division managers (sales, design, safety, quality, purchasing, and engineering) work together to identify project-specific risks and reflect them in construction plans. We also aim to earn the trust of our stakeholders as an honest company by thoroughly complying with laws and regulations and developing employees who have high corporate ethics.


- Quality improvement through DX human resource development
In addition to improving construction quality, we are implementing unique commitments to provide safety, security, and comfort for society.
In the aim of constant self-improvement, we conduct training in pursuit of productivity, quality, and customer satisfaction focusing on DX, including DX promotion leader development, introduction of digital reskilling, and BIM-centric data generation.

- Implementation of on-site patrols
On-site patrols are conducted regularly by employees and subcontractors to check that safety is ensured and that quality and environmental assurance are being implemented appropriately.
On-site patrols by the president and chief general managers of the Taikisha Group are conducted in the aim of creating a system to further accelerate globalization and innovation throughout the Taikisha Group in order to foster a corporate culture and organizational climate where diverse human resources can take on challenges at both domestic and overseas sites.
