Health & Safety Management
Corporate Health & Safety Policy
Basic Principles of Industrial Health and Safety
Based on an understanding of the importance of human life as its basic principle, Taikisha thoroughly implements safety-first planning and construction and fulfills its social responsibilities as a company in the construction industry out of respect for the law. Taikisha aims to protect the health and lives of employees and workers and makes efforts to build a more comfortable working environment.
Action Guidance
- Critical or public disaster prevention
- Development of a comfortable working environment
- Improvement of health & safety management guidelines
- Improvement of health & safety management abilities of overseas group companies
Monitoring of Safety Activity Results
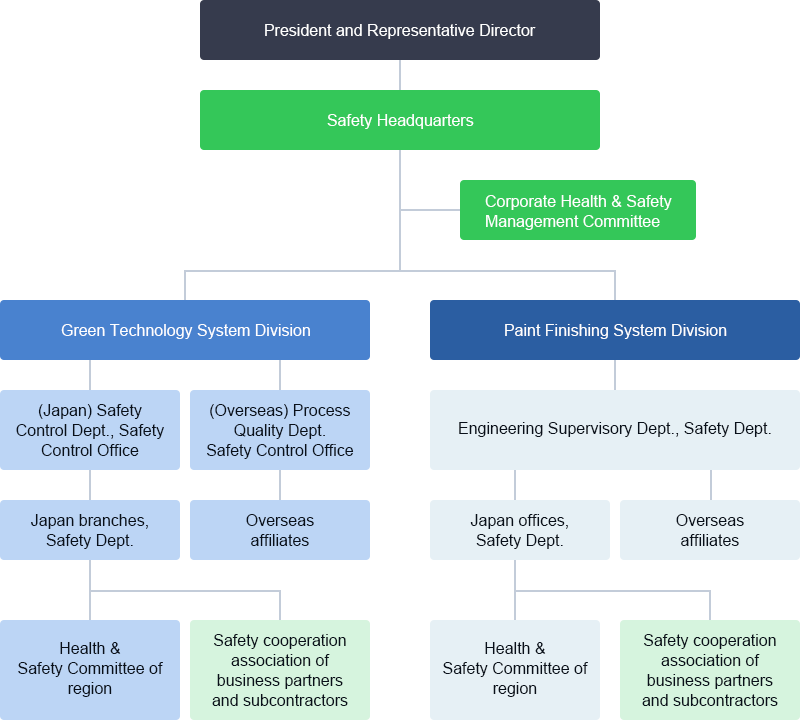
Taikisha has established its own Taikisha Occupational Health & Safety Management System with respect for human lives and a law-abiding spirit as its basic principle.
Taikisha has established the Safety Headquarters in its Headquarters and the Safety Control Department in each of its business divisions, and they support safety activities of Branch Offices and Offices while supervising and managing industrial safety of the entire group.
Health & Safety Management System and Activities
Taikisha measures and monitors the effects of safety activities by using a frequency rate that indicates the frequency of industrial accidents and a severity rate that indicates the severity of accidents as safety indicators. The transition of these indicators is as follows.
Frequency rate: This indicates the frequency of occurrence of industrial accidents, which is calculated based on the number of deaths and injuries due to industrial accidents (accidents involving at least four days of lost work time according to the criteria of the Ministry of Health, Labour and Welfare) per 1,000,000 cumulative hours worked.
Severity rate: This indicates the degree of seriousness of the accident, which is calculated based on the number of work-days lost per 1,000 cumulative hours worked.
Scope: Taikisha's construction sites (employees on a non-consolidated basis and subcontractors)
Frequency and Severity Rate Indicators for the Past Five Years in Japan
unit: %
2019 | 2020 | 2021 | 2022 | 2023 | |
---|---|---|---|---|---|
Frequency rate | 0 | 0.536 | 0.411 | 0.12 | 0.42 |
Severity rate | 0 | 0.010 | 0.022 | 0.001 | 0.043 |
Number of Industrial Accidents Occurred
unit: Cases
2019 | 2020 | 2021 | 2022 | 2023 | |
---|---|---|---|---|---|
Fatal/serious industrial accidents | 0 | 0 | 0 | 0 | 0 |
Industrial accidents involving at least four days of lost work time | 0 | 4 | 3 | 1 | 4 |
Efforts for Accident Prevention
Taikisha created the videos of past accident cases, including crashes and falls, and have begun viewing them to prevent similar accidents. We plan to expand these videos to our overseas offices in the future.
Efforts for Improvement of Industrial Health & Safety Management in Overseas Affiliates
Every two years, the Safety Headquarters conducts an audit of each overseas office and workplace to ensure that they are in compliance with occupational health and safety management activities based on each site's health and safety management system.
Conferences and Safety Training by Inviting Overseas Local Staff
On an annual basis, engineering and safety staff of overseas affiliates are assembled in Japan to be provided with safety education, in an effort to improve their safety management skills. In FY2024, we invited technical staff from overseas affiliates to Japan, and held a meeting of safety managers of overseas affiliates group safety training.
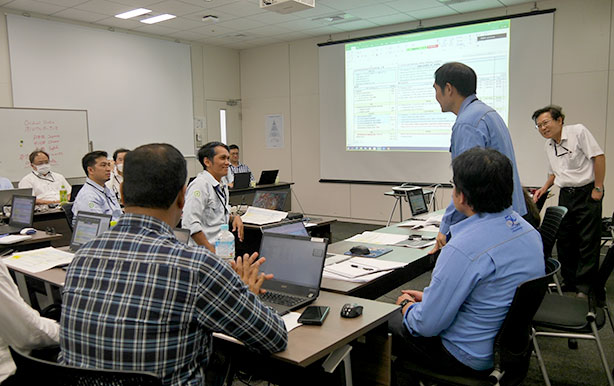
Safety Education Items for Staff Members of Overseas Business Offices
- Safety activity guidance
- Presentation of safety activities of each country
- Group discussion
- Safety patrol training
- Crisis experience training
- Education on various safety management capabilities
- Opinion exchange meeting, etc.
Development of Human Resources for Industrial Safety and Health
Taikisha implements the following initiatives with the aim to develop safety staff in Japan and overseas.
Establishment of information-sharing website for all the safety staff
An information-sharing website was launched for all the safety staff including overseas staff. Safety information and manuals are available in Japanese, English and Chinese.
Staff training on safety
In FY 2023, we conducted five safety training sessions in Japan for 167 young employees, who have been working for four to ten years since they joined the company, as position-specific employee training. We are working to raise the safety awareness of our 1,086 overseas staff by conducting e-learning twice a year and sending safety e-mail bulletins twice a month. In FY 2024, we are planning to conduct safety training, including hazard experiences using VR, for new employees, employees of respective branch offices and bases, and subcontractors. We will continue to conduct e-learning for overseas staff, including distributing a video of some accidents that occurred at our overseas bases.
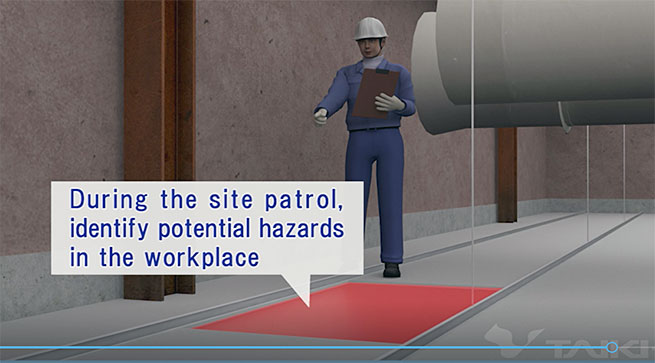
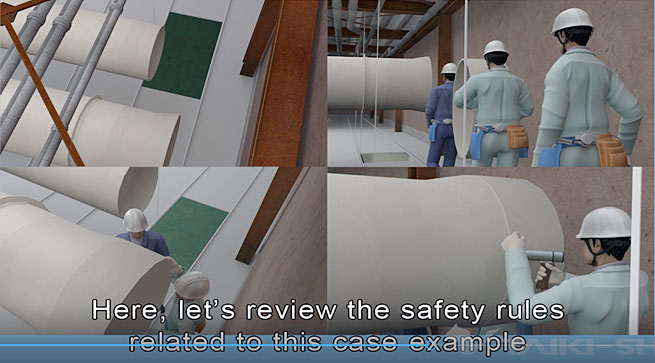
Implementation of general training including safety
The Company set a rule that requires each office, etc. to provide education to its staff and partners about the systems and other matters in accordance with the “education manual for employee preparatory training, business partner training, staff preparatory training and site staff training,” and planned or conducted about 15 different safety trainings at various offices including Safety Headquarters. The Safety Headquarters also conducts training for new staff and new managers as well as various other level-specific training sessions once a year.